Inconel Alloy 825 Welding Neck Flange C276 Inconel 625 Foring Welding Neck Flange
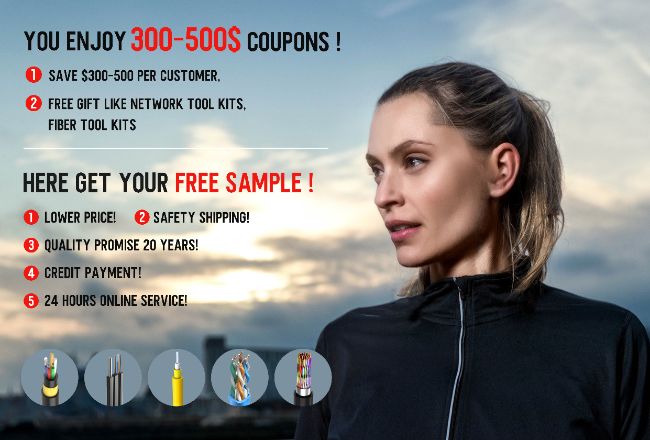
Contact me for free samples and coupons.
Whatsapp:0086 18588475571
Wechat: 0086 18588475571
Skype: sales10@aixton.com
If you have any concern, we provide 24-hour online help.
xMaterial | Alloy 825, Alloy 625 | Type | Welding Neck Flanges |
---|---|---|---|
Standard | EN1092-1 Type 01 | Neck Type | Weld Neck Flanges |
High Light | Inconel Alloy 825 Welding Neck Flange,Alloy 625 Welding Neck Flange,Alloy 825 Welding Neck Flange |
Inconel Alloy 825 welding neck flange c276 inconel 625 foring welding neck flange
Weld Neck Flanges
Weld Neck Flanges are suitable for use in hostile environments that have extremes of temperature, pressure or other sources of stress. This type of flange has been used successfully at pressures up to 5,000psi
A Weld Neck Flange (which can also be known as a high-hub flange or a tapered hub flange) consists of a circular fitting with a protruding rim around the circumference. Weld neck flanges are usually forged and then are typically butt-welded to a pipe which successfully transfers stress away from the flange and onto the pipe instead.
Inconel Alloy 825
Inconel Alloy 825 can be used in many different applications, such as:
- Fuel element dissolvers
- Sea-water-cooled heat exchangers
- Offshore product piping systems
- Heat exchangers, evaporators, scrubbers, dip pipes
- Air-cooled heat exchangers in petroleum refineries
- Chemical and Food Processing
This Nickel-iron-chromium alloy which is a nickel-iron-chromium grade with additions of molybdenum copper, and titanium is a high performing alloy. It is highly resistant to corrosion, with the nickel content sufficient for resistance to chloride-ion stress-corrosion cracking. The addition of molybdenum prevents resistance to pitting and crevice corrosion, while the alloy’s chromium content enables resistance to oxidising substances such as nitric acid, nitrates and oxidising salt.
Inconel Alloy 625
Due to the Inconel Alloy 625’s superior thermal stability, it is often the top choice for those looking for weld overlay applications in the oil and gas, petrochemical and refineries markets.
Inconel Alloy 625 can be used in many different applications, such as:
- Aircraft ducting and exhaust systems
- Engine thrust-reverser systems
- Turbine shroud rings
- Bellows, expansion joints
- Gaskets and damper seals
- Motorsport exhaust and clamps
- Weld overlay and spacers for heat recovery systems
- Furnace muffles
- Valve seats and components
This nickel-chromium-molybdenum-niobium alloy offers the user outstanding corrosion resistance and excellent weldability. The addition of niobium to the alloy delivers high strength but without the need for heat treatment. Like Inconel alloy 825, the high nickel content means that Alloy 625 is immune to chloride-induced stress corrosion cracking. It also has good resistance to pitting and crevice corrosion.